“That top nut is probably the most common problem with any lower-end mass-produced guitar”: Having problems with your shiny new guitar? Try these fixes first
Final quality control on new instruments can vary. Do we all need to learn to do a little DIY?
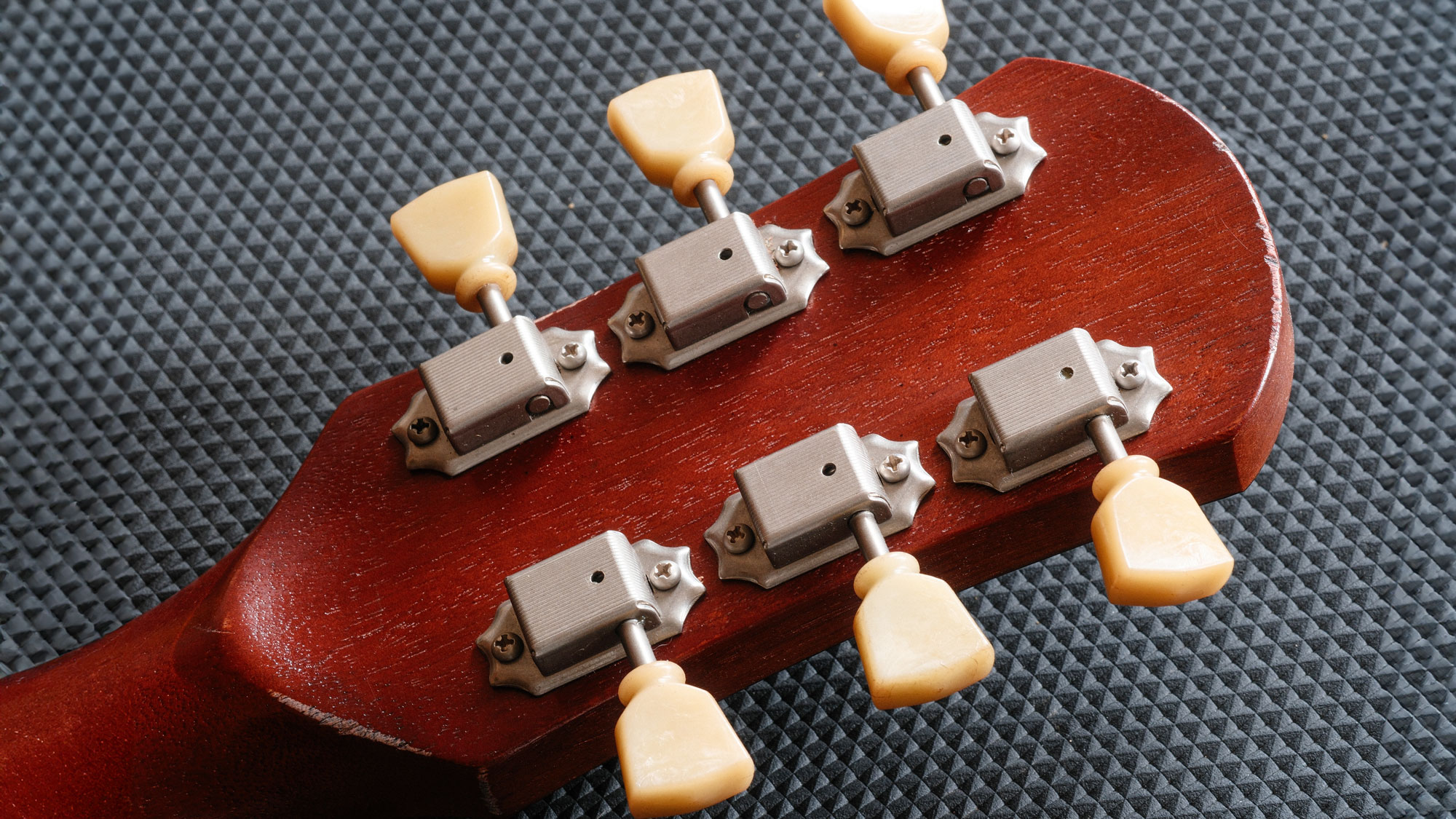
You’d hope that when you buy your shiny new guitar, it would be perfectly ready to go, especially since guitars aren’t getting any cheaper as we’ve all no doubt noticed. Over the past year, however, it’s fair to say rather too many new instruments aren’t quite finished when they turn up at Guitarist HQ.
Is that acceptable today? Do guitar companies think we should either spend our own time finishing off their guitars or pay a professional? Is the quality control of new guitars going down the pan?
It’s impossible to generalise, but a personal bugbear for me is tuning. Can I get the guitar in tune in the first place, and will it stay and play in tune? Now, I’m not expecting to do a quick tune to pitch and then to go off and play an hour’s set without the guitar drifting.
Of course it will. Many of us will have our own preferences for string height and gauge, our own way of attaching strings and stretching them. But when you’ve gone to that trouble and the damn thing struggles to get in tune, let alone stay that way, well, you’ve got trouble.
You’d think price would be the obvious stumbling block, but as we’ve detailed many times there’s no reason a lower-end guitar can’t play like a high-end guitar, though it depends on quite a few factors. Has it been made correctly in the first place with properly selected and dried wood? Not always. And that’s not something we, the end user, can see. But it can certainly contribute to keeping a new guitar in tune. Or not…
Evaluation
As ever, it’s essential to carefully check over any new or new-to-you guitar before you consider any fixes, not least if tuning seems to be a problem. Start with the neck itself. An easy way to test a neck’s stiffness is simply to check whether it moves when you push or pull on the neck in playing position.
Of course, this slight flexing is a technique used by many players to add subtle vibrato. If there’s too much flex, however, you’ve got plenty of potential issues, as with a floating vibrato, where as you raise the pitch of one string, the others will go very slightly flat.
In extreme cases, this will happen as you simply bend one string. The nut therefore has to be very well cut and lubricated, otherwise stable tuning will be next to impossible. A neck with next to zero flex will hold its tuning much better from the off, so long as there are no other issues.
It’s fairly obvious for a less seasoned player to point the finger at the tuners. These devices are supposed to tune the guitar, aren’t they? They must be the problem! But it’s rare that even a lower-end guitar will have dysfunctional machineheads.
They might feel a little stiff or sloppy, but so long as you’ve attached your strings correctly – and stretched them when new – it’s rare that they’re the culprits if you’ve got tuning stability issues, even though that doesn’t stop many people from spending more money on ‘upgrading’ the tuners.
As we’ve often stated, the top nut is typically the real fly in the tuning and tuning-stability ointment. If the string grooves are too tight, they’ll snag the string so a low-fret bend might stay slightly raised, instead of returning to correct pitch. Basic stuff.
Three-a-side back-angled headstocks are especially prone to these problems as the D and G strings in particular splay out from the nut to the tuners, as well as angling down to the tuners. Fender’s six-in-a-line headstocks have pretty straight string pull, but – as with any nut – if those string grooves are too tight, you’ll still have a problem [pics 2 & 3].
Go back a decade or so and it was pretty common to receive new review guitars where the nut was simply left too high, which not only affected the playing feel in lower positions but could also make a simple open E to 1st-fret F, for example, not be in tune as the string will go sharp as you push it down.
The thinking was that the end user might want a different setup or string gauge, and the shop’s tech would make the necessary tweaks before you bought it.
With the advent of online commerce, most (but not all) manufacturers pay much more attention to this, but, to be honest, I’ve lost count of the number of guitars I’ve had on review, certainly in the sub-$/£1k price bracket, that have needed a little TLC in the nut department. Either way, that top nut is probably the most common problem with any lower-end mass-produced guitar. Just saying [pic 4].
At the other end of the string is the bridge saddle. Like the nut, if the saddle snags the string you can have problems. Add in a vibrato to the equation and you have another potential problem.
There’s the fulcrum to consider, the break point on the saddle: is the string catching on the exit point from the block to the saddle? And going back to the headstock, don’t forget that string trees can snag those top strings, too [pic 7].
Bearing all this in mind, you’d be right to expect more potential tuning problems with a Stratocaster or a Bigsby-loaded Gretsch than you would with a Les Paul Junior.
Buzz, Rattle & Hum
Now, even if these elements prove problem-free, a neck needs to be straight (with or without a slight concave ‘bow’, called relief) and the frets level.
Sometimes that annoying buzz you hear might not even be a fret/neck issue; it could be anything from a vibrating spring on a humbucker mounting ring to a loose-fitting truss rod that’s not under tension
If there’s too much relief in the neck when you make those adjustments to the height of the string grooves in the nut and then straighten it, you might well find those nut grooves are too low and you’re now getting string buzz on your open strings. The only fix here is a new nut or a Super Glue drop‑fill. So, yes, there is a process to follow in any instrument setup, old or new.
Buzz, fret ‘rattle’, whatever you want to call it, isn’t always easy to pin down, especially since some of us have heavier picking hands than others. But these technique-related issues – often ‘fixed’ by simply raising the string height and/or going up a gauge of string – can mask the real culprits such as those low nut slots or, obviously, a high fret that hasn’t been seated properly or has become unseated.
Sometimes that annoying buzz you hear might not even be a fret/neck issue; it could be anything from a vibrating spring on a humbucker mounting ring to a loose-fitting truss rod that’s not under tension.
So while playability/tuning issues are the primary issues, that’s not to say there won’t be problems with the hand-wiring that’s in the vast majority of lower-end guitars: switches wired the wrong way around, tone controls that don’t work and, on occasion, loose pots or jack sockets, or a dry joint on an earth wire.
I like to check the electrics and the pickups. I’ve certainly had guitars advertising ‘pickup A’ when the actual pickups are something different.
Case In Point
A recent new launch from a major manufacturer involved three new models being shipped to HQ, review stock for Guitarist, Total Guitar and Guitar World to review. All good – although a couple of reviewers complained about rattles and string buzz. It wasn’t my review, but I asked for one of the guitars to be sent out to me to see what the problem was.
Fair play to our reviewers because ‘rattle and buzz’ was an understatement. The guitar I was shipped was unplayable. Now, I didn’t ask if either of the reviewers had had a go at fixing anything, but it appeared that, at best, the guitar had missed out on a final QC check when it’d landed in Europe, and at worst no-one at the factory had bothered to finish the job or even basically set up the guitar.
Anyway, to sort it out I reset the neck relief, added a neck shim, reset saddle heights and radius, reset the vibrato, reset string heights, recut the top E and B string nut grooves to remove the sitar-like response, and drop-filled the low E nut slot as it had been cut too low.
Personally, I’d have restrung the guitar with a heavier string gauge, too, as it was still quite ‘snappy’ sounding, but that’s a personal preference.
Now, if you’d received that guitar from an online retailer, you’d be sending it back, wouldn’t you? In-store, well, the overworked tech would be tasked to do what I had to do. The thing is, aside from a drop of Super Glue, nut powder and a thin piece of veneer for that shim, the guitar hasn’t changed and yet it’s gone from ‘unplayable’ to ‘perfectly good’.
A sign of the times? I’m not sure. Making a guitar is one thing, and that should include final tweaking and setup, shouldn’t it? I don’t think it’s the job for the end user, or the reviewer, to have to finish it off.
Get The Pick Newsletter
All the latest guitar news, interviews, lessons, reviews, deals and more, direct to your inbox!
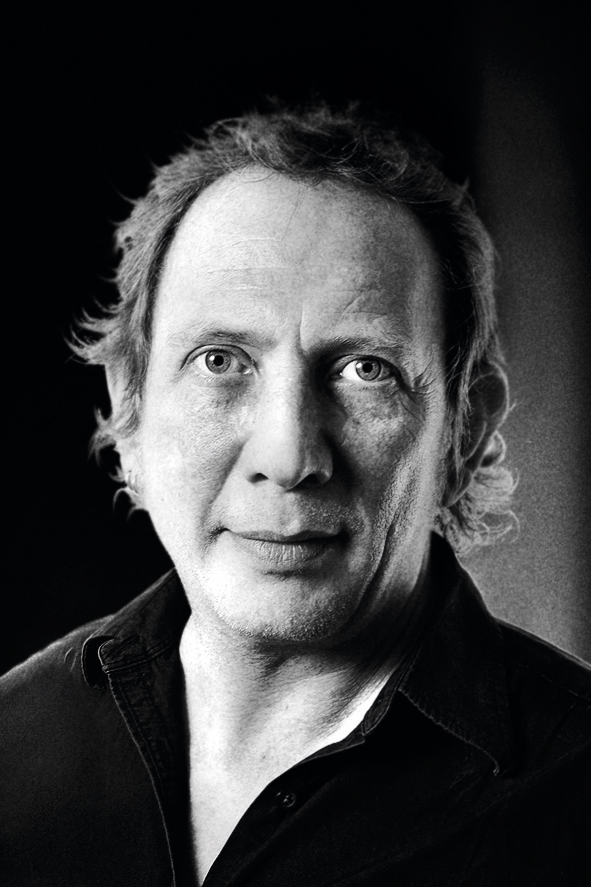
Dave Burrluck is one of the world’s most experienced guitar journalists, who started writing back in the '80s for International Musician and Recording World, co-founded The Guitar Magazine and has been the Gear Reviews Editor of Guitarist magazine for the past two decades. Along the way, Dave has been the sole author of The PRS Guitar Book and The Player's Guide to Guitar Maintenance as well as contributing to numerous other books on the electric guitar. Dave is an active gigging and recording musician and still finds time to make, repair and mod guitars, not least for Guitarist’s The Mod Squad.