“$499 is incredibly high value for a guitar you can go and buy, and go and gig it. And that’s what I want: it’s not a toy”: PRS’ Jack Higginbotham reflects on the history of the SE line
PRS might well be 40 years old in 2025, but the SE guitars seem to be catching up – with a 25th anniversary celebration planned for 2026. Where does the time go?
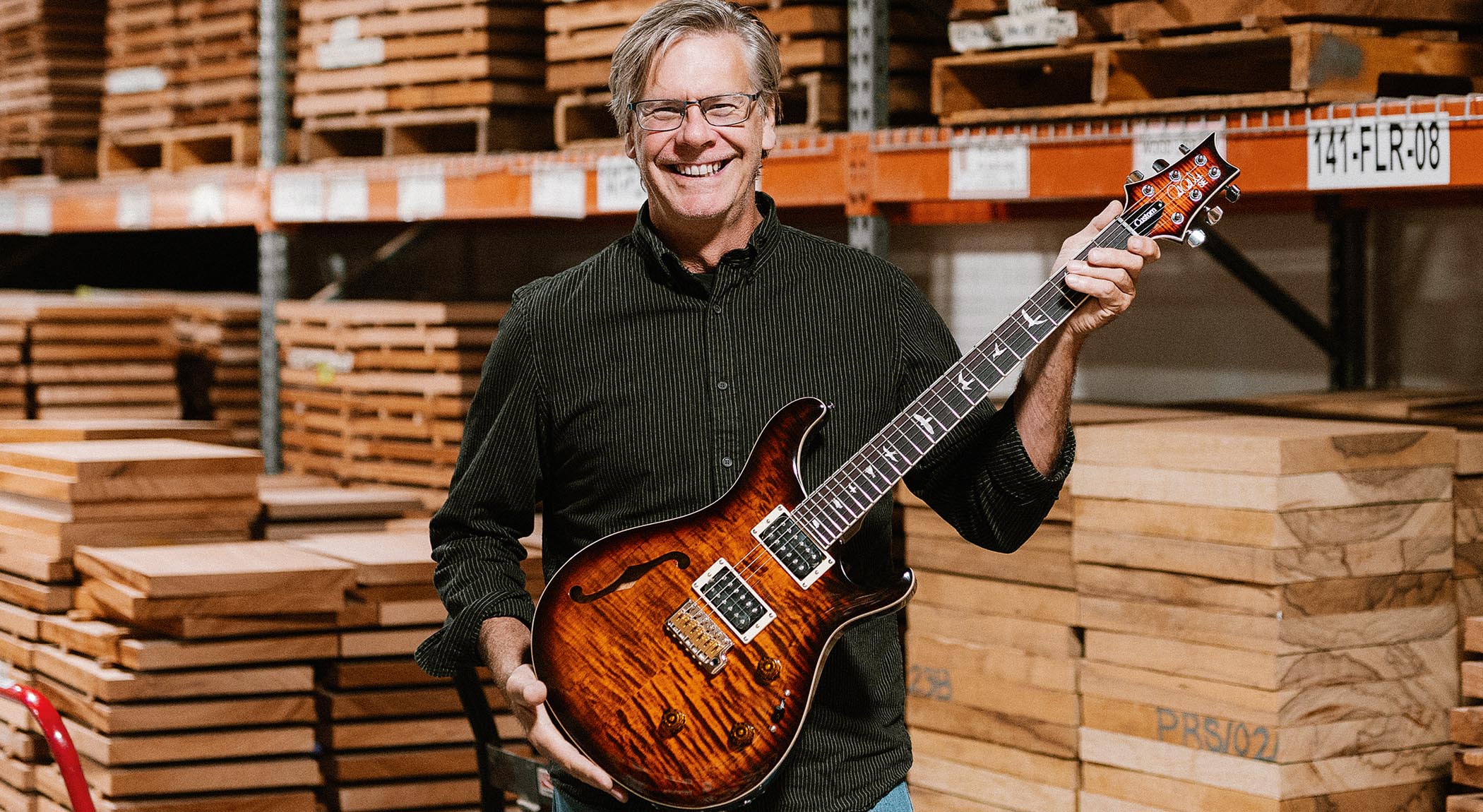
Creating a successful 40-year-old company is far from an easy thing to do, not least in the fickle, often fashion-led world of the electric guitar.
But it won’t be long before PRS’s SE division hits its mid-20s, and in many ways it now seems like a guitar company within a guitar company – not least, of course, that the SEs have always been made ‘offshore’, originally in Korea and now primarily in Indonesia. The SE acoustics and Hollowbodies are made by Cor-Tek in China.
But when the SE line kicked off with a single-guitar introduction in 2001, plenty of people thought it was the beginning of the end, the ‘race to the bottom’ in terms of price and probably quality, and the opposite of the high-level instruments that PRS had been producing in the USA since 1985. Even Paul Reed Smith was hesitant, and models with maple tops (albeit figured maple veneer over solid maple) weren’t initially offered.
But 24 years on from the range’s inception, the revenue that the SEs bring to PRS’s total is now about 45 per cent, PRS’s COO, Jack Higginbotham, tells us.
“I’d say the two tides, if you like, have risen very equally between what we’ve done in the US and what we’ve done in SE,” he says.
Bearing in mind the lower cost of the SE guitars (a quarter, often less, compared with the USA models), presumably to meet those revenue figures, a lot more SE guitars are made annually.
“Yes, by a factor of… a lot!” laughs Jack. “Something like seven or eight times as many, obviously because of the different price points. It’s a lot of units! Until you get used to thinking about it, it’s pretty overwhelming when you start talking about 8,000 of these and 9,000 of those.
Get The Pick Newsletter
All the latest guitar news, interviews, lessons, reviews, deals and more, direct to your inbox!
“I remember a party we had back in the day [27 June 1986, The Night of The 1,000th Guitar]. It was a hard economical time in the world and we were like, ‘Oh, this is a celebration of making 1,000 guitars. What are we going to do now?’”
Making It Work
What they did, of course, is to carry on making guitars. “The thing that’s different is that we are guitar makers, and if we do it well we make money,” considers Jack.
“That’s different from those that go to make money and, in the process of that, make guitars. We make guitars and then we make money. And whether we’re successful or not isn’t necessarily about how much money we’re making; it’s about how much impact we’re having on the instrument, the market and the consumer.
“That’s what wakes us up in the middle of the night, that’s what gets us going. If we have a problem – and everyone has problems in production – we attack it like a fire. We have no appetite for doing anything other than our best.
“On the more practical side, I now have virtually 40 years’ experience of building guitars,” he continues. “The accumulated experience here [at PRS] is like thousands of years, and in order to make a great instrument you have to have a great understanding of what makes a great instrument. You have to understand – through trials and tribulations and mistakes – what to do and what not to do.”
“It literally starts with the wood you select, how you dry it. It’s the thing that not everyone thinks about. You can take a piece of wood that isn’t cured correctly and turn it into the most incredible thing you’ve ever carved in your life, then in three months it’ll be firewood because you didn’t follow the fundamental steps correctly.
What we have is a process that we acknowledge works. It works consistently, it makes the instrument stable
“What we have is a process that we acknowledge works. It works consistently, it makes the instrument stable. We’re following the fundamentals of sound manufacturing guitar principles that allow us to not only make a guitar like this SE Custom 24 Piezo – which technologically is an outstanding thing to me – but also the SE CE Standard bolt-on at $499, which has all the same care and attention to it as this new guitar at $1,599.
“We follow the same process, the same logic, the same mentality. We don’t have two levels of acceptability for the different prices, it’s all the same to me: they’re guitars and they need to be right.
“$499 is incredibly high value for a guitar you can go and buy, and go and gig it. And that’s what I want: it’s not a toy, it’s not for someone to stick in a closet and not use. It has a purpose and that purpose is to make music. And you can’t do that unless you have the knowledge, the patience and the persistence to follow a proper process.”
“Then you have to have the creative side to come up with hair-brained things like this SE Custom 24 Piezo – pushing the envelope. And then there are instruments like the relatively new SE NF3; again, it’s pushing the envelope in terms of its unique pickup design and that’s a good guitar. Actually, I love that guitar! It’s our passion, it’s our purpose.”
Inspectors Assemble
As our reviews attest, not every guitar company feels the necessity to ship us guitars ready to rock. Admittedly, most need little more than a basic setup, but it’s very rare that a PRS SE isn’t anything but gig-ready straight from the box. What’s the process?
“We have a team of inspectors that do that job,” Jack explains. “At the beginning there’s Rob Carhart, our leading product engineer; he does Private Stock, too. Then we have Tom Walls who is our lead inspector; he’s the supervisor of the inspection team.
“He’s just done his third trip to Indonesia to train the builders in the factory to set up the guitars the same way we do here in the USA. He’s training the 40 different assemblers there how to do the job, so when the guitars leave the factory they’re closer to what we want them to be.
”We also have John Walker who literally goes to Indonesia three to four times a year – he’s like my production manager. We have a list with elements we want to work on and we attack the list, and the guitars become better for it. I go to Cor-Tek a couple of times a year myself and do a similar thing.
“Then, of course, the guitar is shipped. Now, if wood is not dried correctly and it sits in a container, which gets up to 150 degrees [Fahrenheit], for two months… very bad things can happen during that journey.
“But we inspect every guitar coming into the US and Canada, and then the team at PRS Europe inspects every guitar coming into the UK and Europe. And our individual distributors are instructed to do the same. We now have PRS in Japan and they’re doing the same thing. It all amounts to quite an incredible cost, but the price of not doing it is higher.”
- “The concept or technology might not be new, but the execution, in such a perfectly made guitar, takes some beating”: PRS SE Custom 24 Semi-Hollow Piezo review
With the initial Covid years now behind us, how is PRS coping with the new landscape? “Everyone acknowledges there was a feeding frenzy during Covid,” states Jack. “We grew significantly, but more importantly we captured market share. If there was a good thing to say about Covid, I think a lot of people thought about playing guitar and picked up on PRS, and understood our mission statement of making a high-value instrument.
“The market today has definitely cooled off from those days, but our company has not significantly cooled off at all. We’re still pushing the same numbers and going after the same things.
“I think it’s harder to sell guitars in the world now than it was three years ago, but I believe that because we have continued to press as hard as we know how on quality and innovation, we’re not getting as much of that [downturn] as many people are. Put it like this: I’ve heard reports and numbers of how much the guitar market is down – and we’re not down by those numbers.”
- For more information on the SE lineup, head over to PRS Guitars.
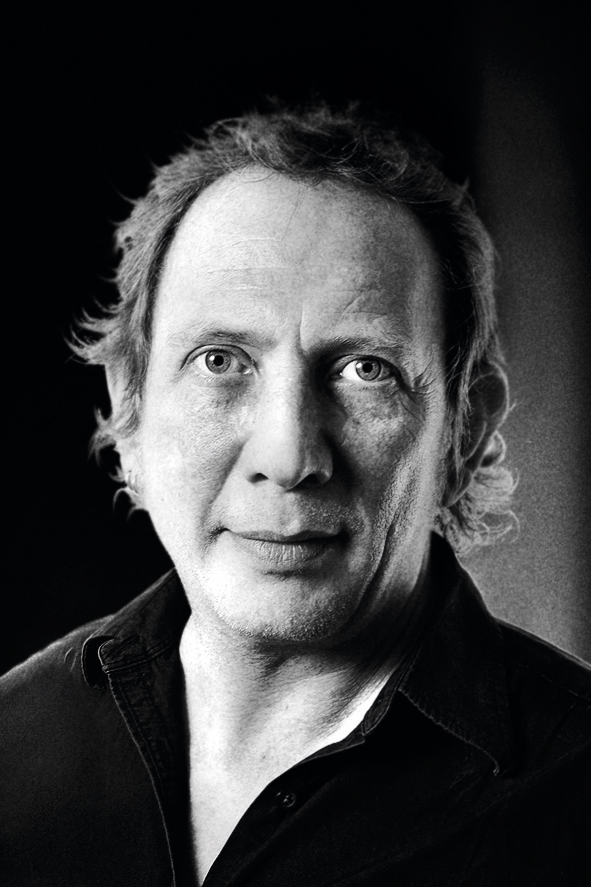
Dave Burrluck is one of the world’s most experienced guitar journalists, who started writing back in the '80s for International Musician and Recording World, co-founded The Guitar Magazine and has been the Gear Reviews Editor of Guitarist magazine for the past two decades. Along the way, Dave has been the sole author of The PRS Guitar Book and The Player's Guide to Guitar Maintenance as well as contributing to numerous other books on the electric guitar. Dave is an active gigging and recording musician and still finds time to make, repair and mod guitars, not least for Guitarist’s The Mod Squad.
Epiphone brings one of Gibson’s most desirable one-off finishes to the masses with Guitar Center-exclusive Widow Les Paul – but it’s been given a twist
Guitar Center’s massive Guitar-A-Thon sale has landed, and there's $600 off one of my favorite Gibson Les Paul finishes and a host of exclusive models from Epiphone, Taylor, and more