“It’s almost impossible for our machinery to make a bad string”: Jim D’Addario on the history, innovations and future of the world’s biggest string manufacturer – and its biggest-selling string sets
As D’Addario celebrates its 50-year anniversary, we speak to its current chairman about the company’s roots, breakthroughs and next moves, and learn how the family has been making strings for centuries
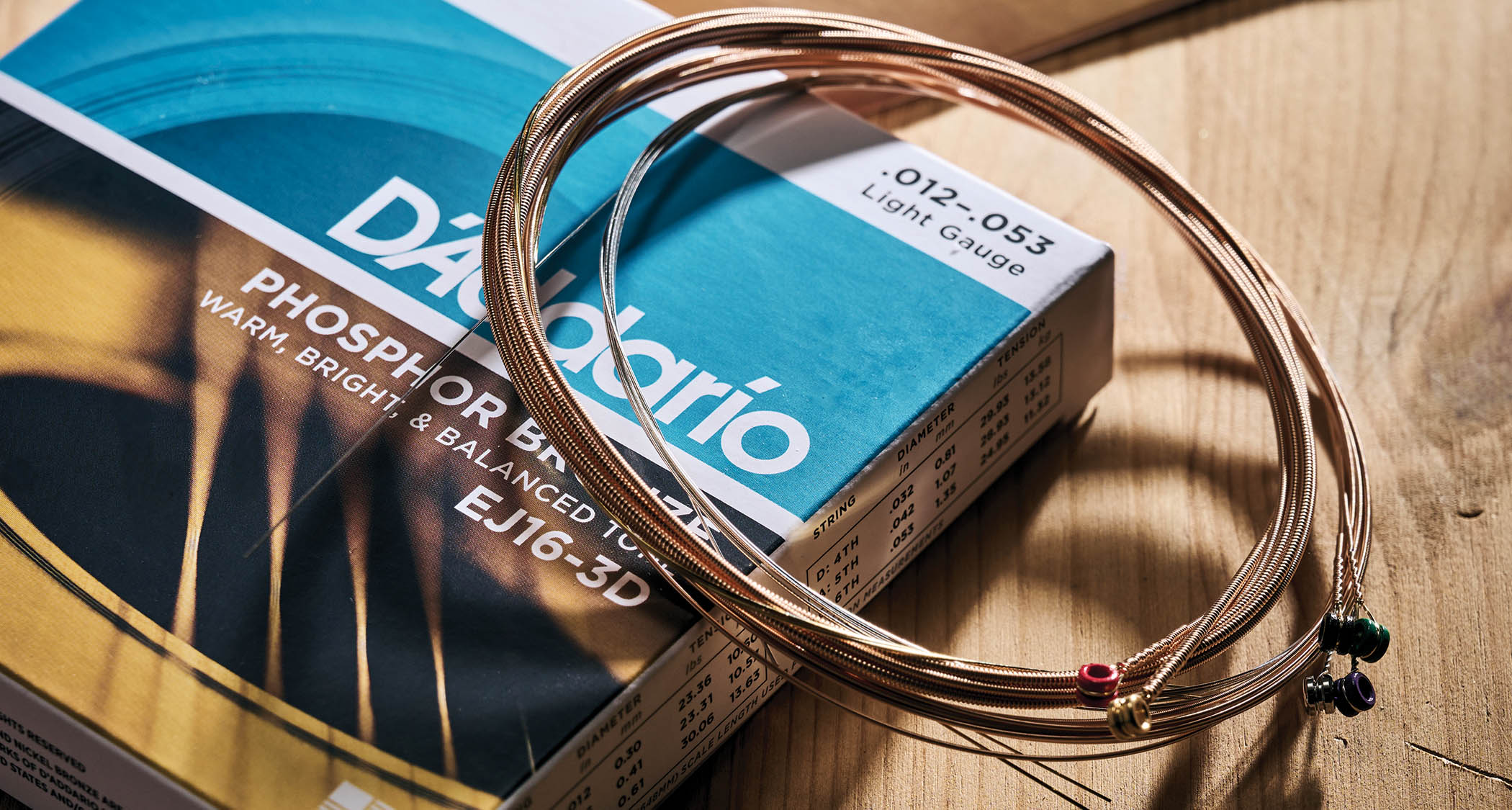
The D’Addario story begins in the Abruzzo mountains of Southern Italy, crosses the ocean to America at the dawn of the 20th century, and writes a new chapter with every pack pulled from the peg of a neighbourhood guitar store.
But alongside the geographical mileage, what resonates with this family firm’s current custodians – chairman of the board and chief innovation officer Jim D’Addario and CEO John D’Addario III – is the relentless march of its product.
From the hard-won intuition of its first string-makers to the forensic accuracy of its cutting-edge wire mill in Farmingdale, New York, D’Addario has remained the market leader since ’74 through its credo that even the most advanced guitar string is a work in progress.
Better materials, tighter tolerances, greater uniformity: all are moving targets that have seen the firm deliver breakthrough products spanning from the XS coated series to the uncanny pitch-holding abilities of the NYXL line – not to mention luring star turns including Nile Rodgers, Mark Knopfler and Guthrie Govan. We asked Jim D’Addario to reflect.
Congratulations on last year’s milestone anniversary, Jim. But the D’Addario story actually goes back even further, doesn’t it?
“Yes. My grandfather [Carmine/Charles D’Addario] came to America in 1905 – at about 14 years old – after there was an earthquake in the family’s hometown of Sala, Italy. He wasn’t really a trained string-maker yet, but there was a shortage of quality strings in America at the time because the recording business was just getting off the ground and there was more need for musical instruments and strings.
“My grandfather started importing strings, but then, during World War I, there were embargoes on importing. So he partnered up with an uncle that knew the trade and he trained him to make strings.
Get The Pick Newsletter
All the latest guitar news, interviews, lessons, reviews, deals and more, direct to your inbox!
“They were partners for several years, and later on he just branched off by himself as C D’Addario. Then my dad joined him in the 1930s when he was in his late teens, and then it was C D’Addario & Son, all the way through to 1959 when my grandfather retired.”
“My dad formed Darco Music Strings, which was a partnership between John III’s dad – my brother, John Jr – and two other gentlemen from the same area in Italy. They were in business for about 10 years, then merged their business with Martin Guitars in ’69, at a time when Martin had made various acquisitions like Levin Guitars and Vega Banjos.
The father always had to put his occupation down on the church records, and it’s ‘string maker’, all the way back to the 1600s. So we’ve been making strings for hundreds of years
“My brother, John Jr, and my dad both had contracts to work for Martin and had to stay for five years. But I wasn’t under contract, so I left in the fourth year and started this company with my wife [Janet], as a printing and marketing company at first. Then, in August of 1974, when my dad and brother were able to join us, we began making strings again.
“We also decided in ’74 that we would use the family name on the strings directly, thus, the 50th anniversary of the brand name D’Addario in 2024. But we’ve subsequently traced our family history all the way back to 1680. The father always had to put his occupation down on the church records, and it’s ‘string maker’, all the way back to the 1600s. So we’ve been making strings for hundreds of years.”
Looking at the timeline from ’74 onward, was there a particular product or string that represents a breakthrough moment for the company?
“There were several, actually, because we were testing new materials all the time and I was very inquisitive about how they affect the string. Of course, it was all trial and error. At the time, we didn’t have a lab like we have now. We couldn’t measure things the way we can today, scientifically, but we did some really innovative things.
“I would say the biggest breakthrough for our company in the 1970s was the Phosphor Bronze acoustic string. Prior to that, various materials were used. The Black Diamond string was the biggest-selling guitar string with a steel core. They started in the 1890s and dominated the market all through the 1920s to 1950s. Then Gibson, Fender and other brands of guitars started to have private-label strings made, or had their own string companies.
“The Black Diamond string was a silver-plated copper-wire string that tarnished early and wasn’t really the best-sounding string on a steel core, but they had a dominant share of the market. Then Gibson put out Mona-Steel, and my dad started developing 80/20 strings – they called it ‘bronze’, but it was really brass – for D’Angelico, Martin, Guild and multiple other companies..”
“The 80/20 was really the benchmark string that my dad developed with John D’Angelico in, like, 1938. Those specifications are very close to what we use today in terms of core-to-wrap ratios and the alloys, but no-one experimented with a lot of different bronzes. They were using what they called ‘bell bronze’. Black Diamond had a bell-bronze string, and I believe that was, like, a 90/10.
“It was 90 per cent copper, a very red-looking alloy, and it didn’t really sound great. A lot of that had to do with the fact they didn’t really have sophisticated machinery… So, even though it looked like a string, it didn’t have the performance that we expect today from strings. The whole state of the art of making strings has improved so dramatically.
“So I would have to say the Phosphor Bronze was the big one. The second biggest was our Half Round bass strings in 1975. The whole world was migrating more towards a round-wound, brighter sound, even on the bass, when people like John Entwistle were making it more of a solo instrument. When we introduced those, they were a big success.”
Is it harder to make a good electric string than a good acoustic guitar string?
“They’re pretty much the same in terms of the process, winding techniques and so on. What is different is specifying the material, and the temper it needs to be annealed or softened to after drawing it. We did a lot of trial-and-error testing.
“We weren’t as sophisticated as we are today, but when I purchased our first Instron tensile-testing machine in the early ’80s, we realised, ‘Oh my God, these people are just making the wire any which way they wanted.’ It was like they didn’t ask you whether you wanted your steak rare – you just got steak!
“We started doing blind acoustic testing of the various alloys in the ’80s. We spent a lot of time A/B testing, without telling people what they were playing.
“We varied the tempers and discovered that having that wire tempered to the ideal temper for the particular type of string – whether it’s an acoustic or an electric string, whether it’s a Phosphor Bronze instead of an 80/20 Bronze – they are all slightly different. Those slight variations in the way you temper it make a pretty big difference with the performance.”
If you can believe it or not, we sell quite a bit of wire to our competitors
“Having the good fortune to afford a machine to do that testing, we honed in on where we wanted to be with those wrap wires. Now, we have a wire mill here in Farmingdale, where we make almost all our wire, both high-carbon steel for the core and plain strings, and wrap wires. We make nickel-plated steel for electric, Phosphor Bronze and 80/20 for acoustic.
“We’re able to zone in with the equipment we have today. It’s all digital. In a lot of cases, we’re not even using traditional ovens to temper the wire. We’re using plasma on one line and induction on another. You can control the temper so precisely, you don’t have to be concerned that it’s varying and that you might be getting different strings from the output of your factory.
“It’s one of the reasons why we decided to invest in a wire mill and grow that, and it’s a pretty nice operation that we have there. If you can believe it or not, we sell quite a bit of wire to our competitors.”
Can you tell us a more about your wire mill operation – and how it has improved the quality of the D’Addario product?
“About 10 years ago, we moved the wire mill we had in Massachusetts down to here. But we essentially discarded all the equipment and bought all-new, super high-tech German wire-drawing machines, four of them to start with. We now have six of those for high-carbon steel and three more for wrap wires, so we have nine lines running [and a 10th to come].
“We immediately started experimenting with the high-carbon steel back then to see if we could just tweak that tensile up a little bit. We were fortunate enough to make it about 10 per cent stronger, so it stays in tune better.”
“We also developed the Fusion Twist, where the twisted area of the ball-end is fused so it doesn’t slip. The NYXL was the first set we introduced with this new wire, and the tuning stability was really noticed by the consumers. Pat Metheny said, ‘It does away with the need for my roadie to tune my guitar after I play a wild song’ – and it’s true.
“We wouldn’t have had that opportunity if we didn’t make our own wire mill because none of the vendors were capable, or interested, in doing anything like that. [This was] because the quantities of wire the music industry uses is pretty small compared with electronics, automotive and that kind of thing.
“High-carbon steel is used in steel-belted radial tyres – imagine how much more high-carbon steel is produced for the tyre industry than the string industry, right?”
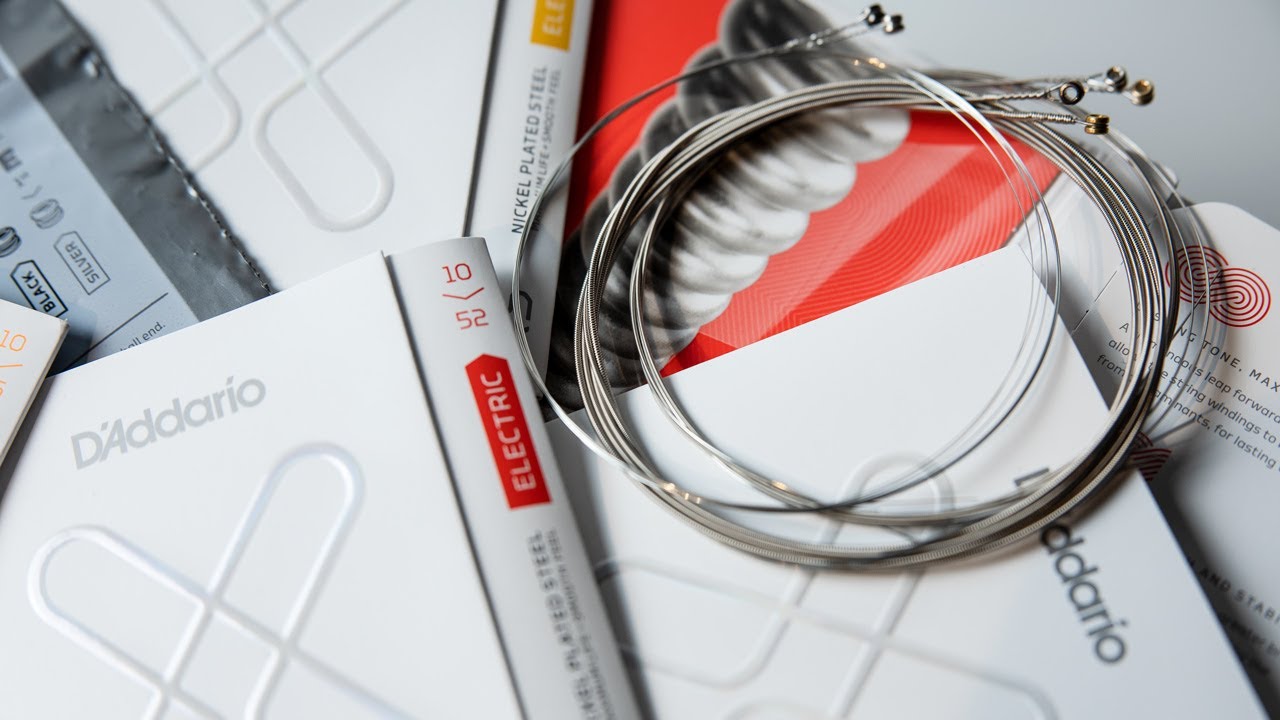
You mentioned Pat Metheny. What role have artists played in making significant advances in D’Addario’s product line and its quality?
“They’re a very important factor. We do a great deal of testing with our artists – and I’m not going to say that some are ‘better’ at it, but they’re more valuable testers because they actually take a more objective and scientific approach to evaluating what you’re asking them to test. Other people are sometimes not as discriminating – or sometimes overly discriminating. They’re great players, but they’re not great testers, right?
“Then there are people you know you’re getting a reliable answer from. Pat is one of them. He’s one of those guys that, when he tests something of yours, it usually correlates with the scientific knowledge we already had about the product we asked him to test.”
What trends have you seen over the years, in terms of string gauges and their suitability for various acoustic body types?
Doc Watson used to get our heavy-gauge 80/20 strings. It’s like playing ropes! It’s a lot of work, but they drove those guitars and made it possible for you to hear them
“Well, when I first started playing acoustic guitar in the 1960s, they were just starting to monkey around with piezo pickups – Ovation really being the first electrified acoustic guitar you could take on stage and have a semi-decent tone through the pickup system they developed.
“Prior to that, everyone was standing in front of a microphone. So if you watch Bob Dylan or Pete Seeger, they’re standing there in front of a microphone and trying to maintain the right distance.
“Very tricky to get really great tone out of the guitar, so everyone was always gravitating towards large dreadnought Martins, right? Because they were louder. But you see a lot of people now playing 00s and parlour-size guitars because the pickups and strings are much better.
“The fact is that some of those guitars speak better in the midrange, particularly if you’re a soloist or your particular type of songwriting uses those middle strings. We don’t even sell heavy gauge much any more. Doc Watson used to get our heavy-gauge 80/20 strings. It’s like playing ropes! It’s a lot of work, but they drove those guitars and made it possible for you to hear them.
“Now, that has changed dramatically because there are so many other tools. You have different sound effects, pedals and amplifiers to tweak the tone, and these smaller guitars sound wonderful on stage. You don’t really need a thicker string.
“Our biggest-selling set is our 012 Light Gauge. But I always made, for myself, a set which is like our EJ26 set, which has an 11 and 15 on the top. Then the rest is almost the same as the EJ16 Light Gauge set.
“I always liked that better because the top string spoke better for me, and I could bend them a little bit. Of course, all the ageing baby boomers like me, we’ve got arthritis in our fingers now, so we’re not going to play medium-gauge strings any more anyway because they hurt to play!”
Right now, it feels as though acoustic singer-songwriters are the most prominent guitar practitioners. Is that reflected in relative sales of electric and acoustic strings?
In all honesty, the sales of acoustic guitars right now are sluggish. Factories are not running at capacity, but that doesn’t mean people aren’t playing the same amount of acoustic guitar
“We were always known for the acoustic strings first. But now, recently, with our NYXLs and our XS coated electric strings, we have a first position in almost every category of string.
“In all honesty, the sales of acoustic guitars right now are sluggish. Factories are not running at capacity, but that doesn’t mean people aren’t playing the same amount of acoustic guitar.
“I think the problem we have now is you compete with used instruments, as a manufacturer, particularly acoustic instruments, in that they actually sound better when they’re older, right? So people don’t put the guitar in the basement, next to the boiler, and watch it crack or put it in the attic. They put it on eBay or on Reverb – and get their money back!”
Finally, what do you think are the most promising areas for the further evolution of guitar strings, whether for acoustic or electric?
Those ‘aha’ moments are few and far between now because we’ve all turned over almost every rock in the garden, looking for worms
“I would even spread it out a little further because one of the things we’re working on is a way to come up with a covered classical guitar string. That’s a real challenge because the core melts in the process of fusing the coating, so we have to come up with a different coating that would actually function at a lower temperature.
“We’re working hard on that because we think the coated wound strings on a classical guitar string would be a big seller for us. We have a lion’s share of the classical guitar-string market worldwide. In fact, two out of 10 of our top-selling sets of strings are classical guitar sets, believe it or not.
“I think we’re at a point where we’ve explored almost all the materials that are viable. Those ‘aha’ moments are few and far between now because we’ve all turned over almost every rock in the garden, looking for worms. So now our opportunities are about process.
“What we’ve done on our machinery and everything else is to incorporate sophisticated digital controls and measuring sensors and devices everywhere so that every string comes out the same. It’s almost impossible for our machinery to make a bad string.”
- Find out more at D'Addario.
Henry Yates is a freelance journalist who has written about music for titles including The Guardian, Telegraph, NME, Classic Rock, Guitarist, Total Guitar and Metal Hammer. He is the author of Walter Trout's official biography, Rescued From Reality, a talking head on Times Radio and an interviewer who has spoken to Brian May, Jimmy Page, Ozzy Osbourne, Ronnie Wood, Dave Grohl and many more. As a guitarist with three decades' experience, he mostly plays a Fender Telecaster and Gibson Les Paul.
You must confirm your public display name before commenting
Please logout and then login again, you will then be prompted to enter your display name.
“A distinctive brightness that no other strings have been able to capture”: How Rotosound revolutionized the bass world with its Swing Bass 66 strings – and shaped the sound of rock music in the process
“I’m not going to say that some are ‘better’ at it, but they’re more valuable testers”: D’Addario recruits players to help test its strings – and there's one jazz veteran who is more reliable than most