Their job titles are ‘Wrangling Hellcat’ and ‘Waste Management’ – meet the multi-talented minds behind Jack White’s fast-rising pedal brand, Third Man Hardware
Dan Mancini shares the stories behind the collaborations that have helped White and Third Man Hardware to demand attention from players of all, er... ‘stripes’
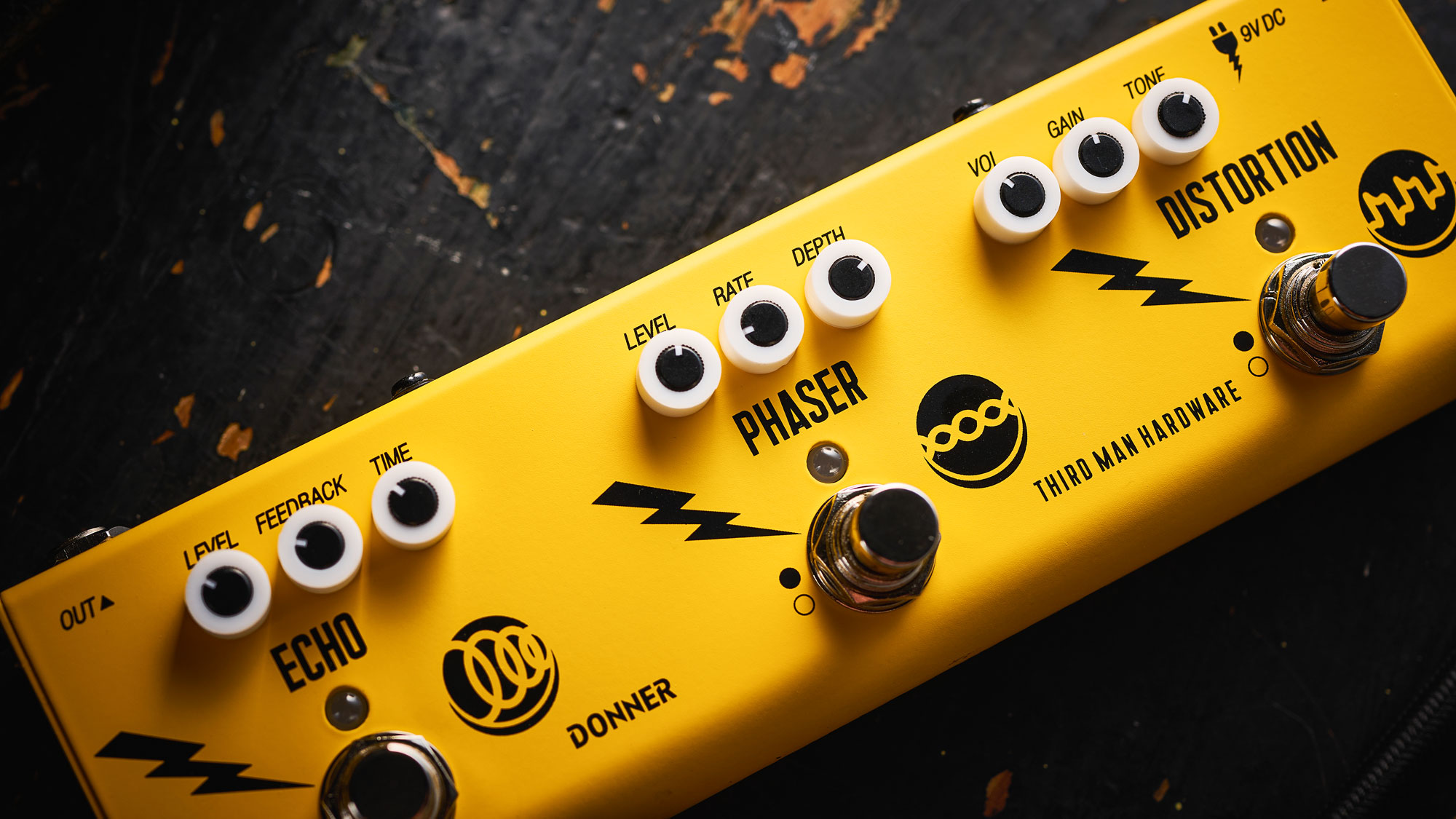
Not many pedal companies have the luxury of road-testing their products. Then again, not many guitar pedal companies are run by Jack White. The team at Third Man Hardware is – perhaps surprisingly – small. Of course, there’s White, the creative heartbeat of all things Third Man. Then there’s Christina Inman and Dan Mancini.
Inman, whose official job title is “The Wrangling Hellcat,” handles most of the business side of Third Man Hardware while also managing merchandise for Third Man Records. Mancini, who describes Inman as a “total badass,” has a Third Man business card that reads “Dan Mancini: Waste Management.”
Though these job titles might seem arbitrary, they actually reflect the many hats Third Man employees wear.
For instance, when Mancini isn’t repairing and maintaining gear at Third Man’s Nashville studio (as his job title suggests), he’s on the road as White’s guitar tech, crash-testing prototypes he’s helped develop for his day job at Third Man Hardware.
You’d been Jack’s tech for a number of years before you got started with Third Man Hardware, right? When did that happen?
“It was 2019, when we were still developing the Triplegraph with the Coppersound guys. Jack had already done one or two pedals with Third Man Hardware before. We were going out with the Raconteurs, and I started helping in the final stages of development with little odds and ends.
“Christina had been helping keep the project moving along, asking me lots of questions along the way. Slowly, everyone was realizing I was a pretty good fit to help make things happen. [Now] I help out with the development and the technicals and creative elements of the gear with Jack.”
Get The Pick Newsletter
All the latest guitar news, interviews, lessons, reviews, deals and more, direct to your inbox!
How was the Triplegraph developed?
“That was four years in the making, and it was something Jack had cooked up with the fellas. Coppersound sent, like, a little Morse Code pedal, just a single little killswitch. They just sent it to him, thinking he’d get a kick out of it. He loved it.
“Visually, it’s really appealing and it’s fun. In the White Stripes and on his more current guitars, like the Triplecaster, he loves killswitches. But then he wanted to take a step further, and he said, ‘It’d be cool if we actually put on three of those, and there were two octaves on it, and the killswitch or a looper in the middle.’
“They just chipped away at it over the years. We crash tested it with the Raconteurs [in 2019]. We had a prototype on the board, and over that last year or so we kind of really honed it and got it past that finish line. That was a really wacky one to put out. I’m glad it landed like it did.”
The Knife Drop is another kind of “out there” or unique collaboration, like the Triplegraph. How did that come to fruition?
I was like, ‘Damn, this is some wild shit!’ I took it to Jack and said he needed to hear this ‘Knife Drop’ setting and he loved it
“At a couple points, Eventide had sent out a couple of pedals they wanted to try and develop with us. We couldn’t find a path with those immediately. They sent us another one later on, the H90 Harmonizer. It’s pretty funny. I get a little bit of digital anxiety with overly computery pedals. You get lost. You lose your settings.
“I’m always a little skeptical of those. But they sent the H90 over and I plugged it in at the studio and I started messing around. I found a couple settings and I was like, ‘Damn, this is some wild shit!’ I took it to Jack and said he needed to hear this ‘Knife Drop’ setting and he loved it.
“So we said to Eventide, ‘Hey, I don’t know that things are working out with this pedal, but what if we tried taking this Knife Drop sound and put it into one of your enclosures that you already make?’
“I think that one took about a year or so. We tried simplifying it as much as we could on our end. For instance, taking it from their six-knob enclosure and reducing it down to three. Those six knobs still exist, but you have to hold a button and dive down the rabbit hole.”
“Also, we really were fixated on the idea of always being able to get back to that core sound, so we ended up building in a cool little back door where you can hold the right toggle switch for, like, two or three seconds and it’ll always come back to Knife Drop. So no matter how much you mess with all these settings, or say, kick your knobs on stage, all you gotta do is hold that switch for a couple seconds and boom, you’re right [back] there.
“We had so much fun doing all the artwork, too. We did that with Rob Jones, who’s been a collaborator of Jack’s for years, all the way back to the White Stripes days. He’s done lots of posters and merch and all that stuff. That was a fun journey.”
With the small team and the way things are handled in-house, there’s definitely a DIY ethos to Third Man Hardware. Is that right?
“You’re totally right. I mean, the whole DIY element is why Third Man exists. Many of the people who work at Third Man are there because they all played in bands and put out their own records and made their own T-shirts. We do as many things in-house as possible. So that’s definitely a thread going through everything.”
How does that extend to the pedals you make? Is that why the Fuzz-a-Tron was developed, for example?
“Yeah. With the Fuzz-a-Tron, we really wanted to do something at a lower price point that also got people inspired. [We’ve done] a bunch of boutique American collaborative pedals that were fun, but obviously, a little on the pricier side because of the small companies, and they’re American made and all that.
“We really wanted to sow those seeds of creativity in people. You know, we’re all people who fix stuff and solder away. For the Fuzz-a-Tron, we wanted to empower people to think, ‘Oh, I can fix my input jack!’ or ‘Oh, yeah, I can fix that. It’s just, fix the battery lead.’”
‘Bill Skibbe, who does Third Man Mastering, has his own electronics company. Back in the late ’90s, he tried doing a kit with a company called Heathkit, who is a Michigan-based company. They have great instruction manuals and you put the stuff together yourself. [That project] never got off the ground.
“It was basically a Mosrite Fuzzrite clone. It sat in his garage for years. So a year and a half ago, we started kicking our own ideas of what to do next and how we want to start making more of our own stuff. Bill said, ‘Oh, maybe we could try and do this Fuzz-a-tron. It’s this Heathkit thing that I tried doing years ago that never took off. Maybe we can pump some life into it.’”
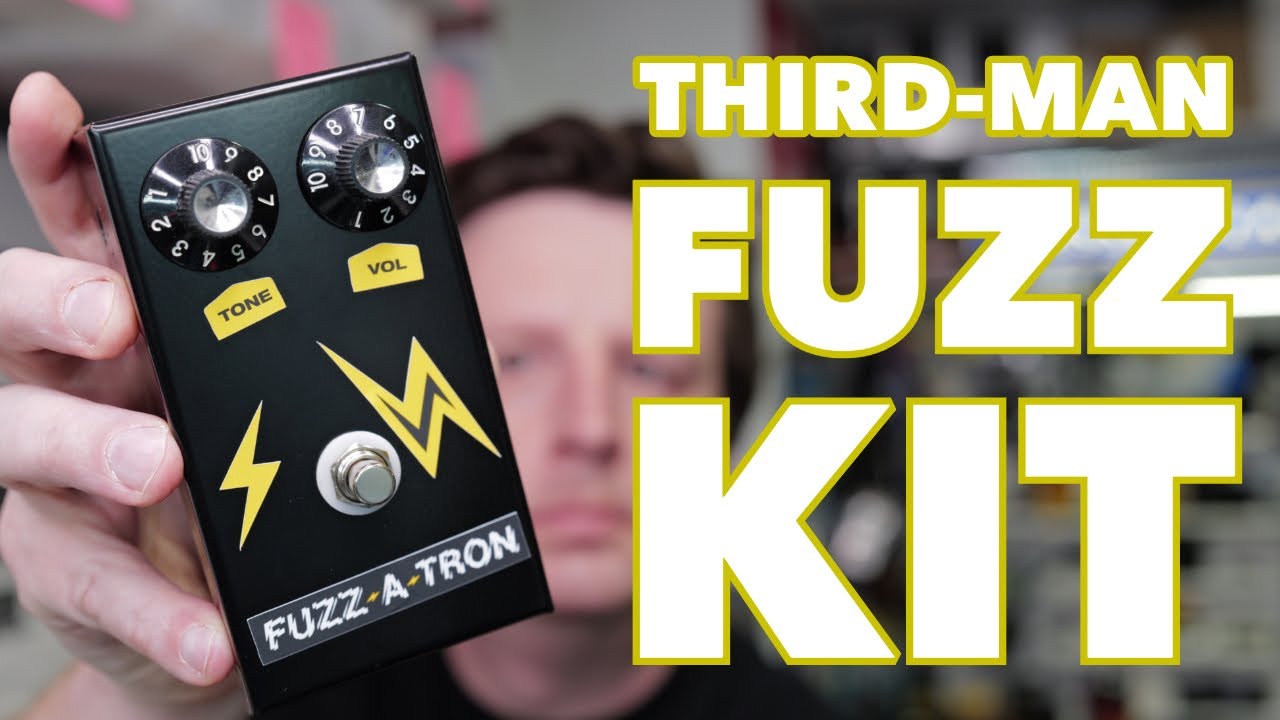
“Bill had 85 to 90 percent of it kind of cooked up, but then I ended up testing out a couple other things in the circuit. You know, you can’t find all those components anymore, so we had to adapt it a little bit. We tried out a bunch of stuff over at the warehouse and cooked up a nice manual. Some DIY kits can be kind of cold and uninspiring and too technical and everything.
With the Fuzz-a-tron, we tried our best to make it inviting. We wanted a no-fail fuzz kit that people of any budget or experience can get excited about
“With the Fuzz-a-tron, we tried our best to make it inviting. We wanted a no-fail fuzz kit that people of any budget or experience can get excited about, and hopefully have a ‘win’ with electronics. Hopefully people think, ‘I could be a person that has a little tool bench and solders away in my garage and makes cool stuff.’
“It’s as basic and as fail proof as you can get in a pedal where it’s, like, four resistors of the same value, four capacitors. It gives you the opportunity to really imagine my little electrons are making their way in here, and we’re making them do this little dance through circuits and put it right out the back end. It really demystifies a lot of it.”
- “For players who want to get lairy, experiment with the interactions between stompboxes, and create auditory chaos”: Eventide x Third Man Hardware Knife Drop review
- This article first appeared in Guitar World. Subscribe and save.
You must confirm your public display name before commenting
Please logout and then login again, you will then be prompted to enter your display name.