“We’ve been controlled by the idea that Fender is for Mexico and US models. We’re allowing ourselves to break our own rules”: Why Fender is building its $599 Standard Series in Indonesia – and how its ideological shift delivers better value for players
Fender’s EVP of Product Justin Norvell explains what convinced Fender to change its mindset on where its guitars are built – and what makes the new Standards different from the Player Series (apart from where they’re built)
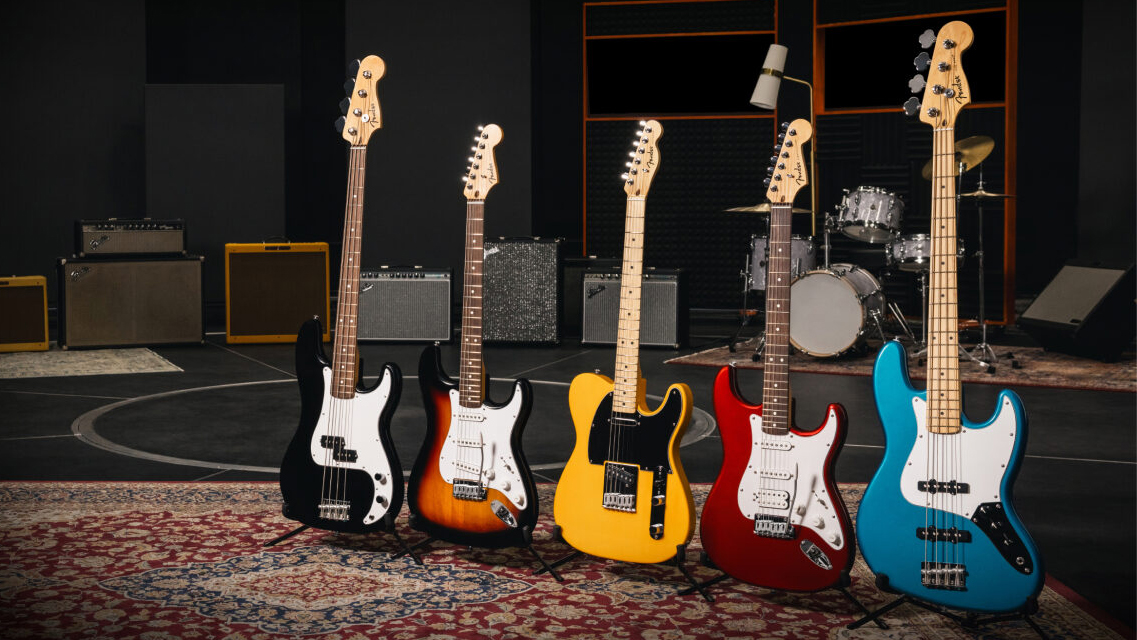
One of the biggest surprises of NAMM 2025 was the announcement of an all-new, Indonesian-built Fender Standard Series, with models starting at $599.
The relatively no-frills range – consisting of a Strat, Strat HSS, Tele, P-Bass and Jazz Bass in four classic finishes each – was introduced to fill the gap between the Player II Series, which kicks off at $799 and the Classic Vibe range from Fender’s budget brand Squier, where prices top out at $449.
All of which makes the Standard Series the new cheapest entry point to the Fender name.
But the use of an Indonesian factory to build Fender guitars has raised a few eyebrows among guitar players used to only seeing the Big F on America and Mexico-built instruments.
However, as we’ve previously observed, Fender has been quietly moving in this direction over the past year, with more expensive guitars, including the Tom DeLonge Starcaster and Jim Adkins Telecaster, now coming out of Indonesia. And there’s past form, too – for example, the 2011 Modern Player line, which was built in China.
Nonetheless, building an entire range in Indonesia signals a shift for the company, and carries implications for its future moves – particularly in the face of recently threatened tariffs on Chinese and Mexican imports to the US.
At NAMM, we caught up with Fender’s EVP of Product Justin Norvell, who gave us the lowdown on the internal machinations behind the new range.
Get The Pick Newsletter
All the latest guitar news, interviews, lessons, reviews, deals and more, direct to your inbox!
“I think we have been maybe overly dogmatic or just controlled by the idea that Fender is for Mexico and U.S models,” he says. “The way things are these days, it’s not about what factory it’s made in.
“It’s really like, ‘Squier goes to 500 bucks in the US, and Fender should start there and go up.’ And so we kind of just got out of our own way, I guess.”
By changing the perception – internally and externally – of what makes a Fender guitar, Norvell says the firm aims to deliver more competitive prices for guitarists.
“In our head we had drawn these indelible lines. And now it’s like, ‘What makes the most sense, when doing a guitar?’ If we did that [Tom DeLonge] Starcaster in Corona or in Ensenada, [the price] would not have come in where it did [at $1,199].
“We just thought that the time was right to get out of our own way and say, ’This is how a product line should look, and this is what we think people would want.’ And then we figure out where it’s going to be made.”
The Acoustasonic Standard – the company’s most affordable take on the hybrid acoustic-electric yet – is a case in point, and an example of how this new way of thinking can deliver the right guitars at the right prices.
“The original Acoustasonic was a little under two grand. Then the made-in-Mexico one, we wanted it to be under a grand, and it was like 1,200 bucks. The new one is $600 and that’s where it needs to be. A lot of times we’re allowing ourselves to break our own rules, and just do what people want.”
On paper, few players would argue with a new series of $599 Fender guitars, but the company wanted to get it right, especially with increased scrutiny over the new country of manufacture.
Several years of R&D went into the lineup, and although internet commentators may have you believe the new models are just rebadged Squiers, it was important to make a clear distinction with the firm’s budget brand, says Norvell.
“We didn’t want to take a Squier and put ’Fender’ on it. So we spent considerable time in the factories and in design, figuring out what that would be – and what the specs would end up shaking out as – to make it make sense and have a reason to exist, but still be compelling.”
Where the Squier Classic Vibes pay homage to vintage specs and the Player II is more contemporary, the Standard Series exists, says Norvell, to be a “good today’s Strat, Tele, P-Bass, Jazz Bass”.
So, Classic Vibes have gloss necks and vintage-style tuners, whereas the Standards have satin necks, sealed tuners and two-point tremolo systems, alongside poplar bodies and ceramic pickups.
An extra $200 spent on the Player II Series, meanwhile, gets you a much wider range of colors, alder bodies, Alnico pickups and 18:1 tuners.
There’s a clear spec differential between each range. As Norvell says, “We’re not just plugging holes.”
And for anyone who’s sceptical of the quality of the instruments coming out of the Indonesian factory, which is led by manufacturing giant Cort, Norvell is quick to point out Fender’s long history at the facility.
“These aren’t factories we’re just outsourcing things to; they’re factories that we’ve been working with for 25 years. We would send teams of our own luthiers and quality inspectors, too. And we’ve trained many of these factories on how to build guitars that other manufacturers also use.”
Ultimately, Fender’s move is a reflection of the changing importance of country of origin when it comes to guitar building, especially when the likes of Epiphone and Eastman are producing premium guitars in China, with price tags of over $1,000.
We were making guitars in America, then Japan, then we went from Japan to Korea, Korea goes to Indonesia or China. It’s just the way guitar making has gone
Meanwhile, budget brands such as Harley Benton and Donner are making instruments with price tags that significantly undercut offerings from the big American firms.
But this isn’t Fender’s first rodeo. Its first Japanese-built models were introduced to deal with cut-price copies, and this is the latest step in its quest to ensure Fender remains “the working (wo)man’s guitar”.
“Country of origin means something in certain cases, like Custom Shop and things of that nature, but to a large extent, people just want great guitars and great value,” Norvell concludes.
“And so that’s what we’re trying to do. That’s why we opened Mexico back in 1985, and it’s just going to continue to extend. We were making guitars in America, then Japan, then we went from Japan to Korea, Korea goes to Indonesia or China. It’s just the way guitar making has gone.
“Many people are making guitars in China and Indonesia that are over a thousand dollars. So that whole thing has kind of blown up. Because if the quality is there and it’s a great guitar, it’s worth it.”
- For more info on the Standard Series, see Fender.com.
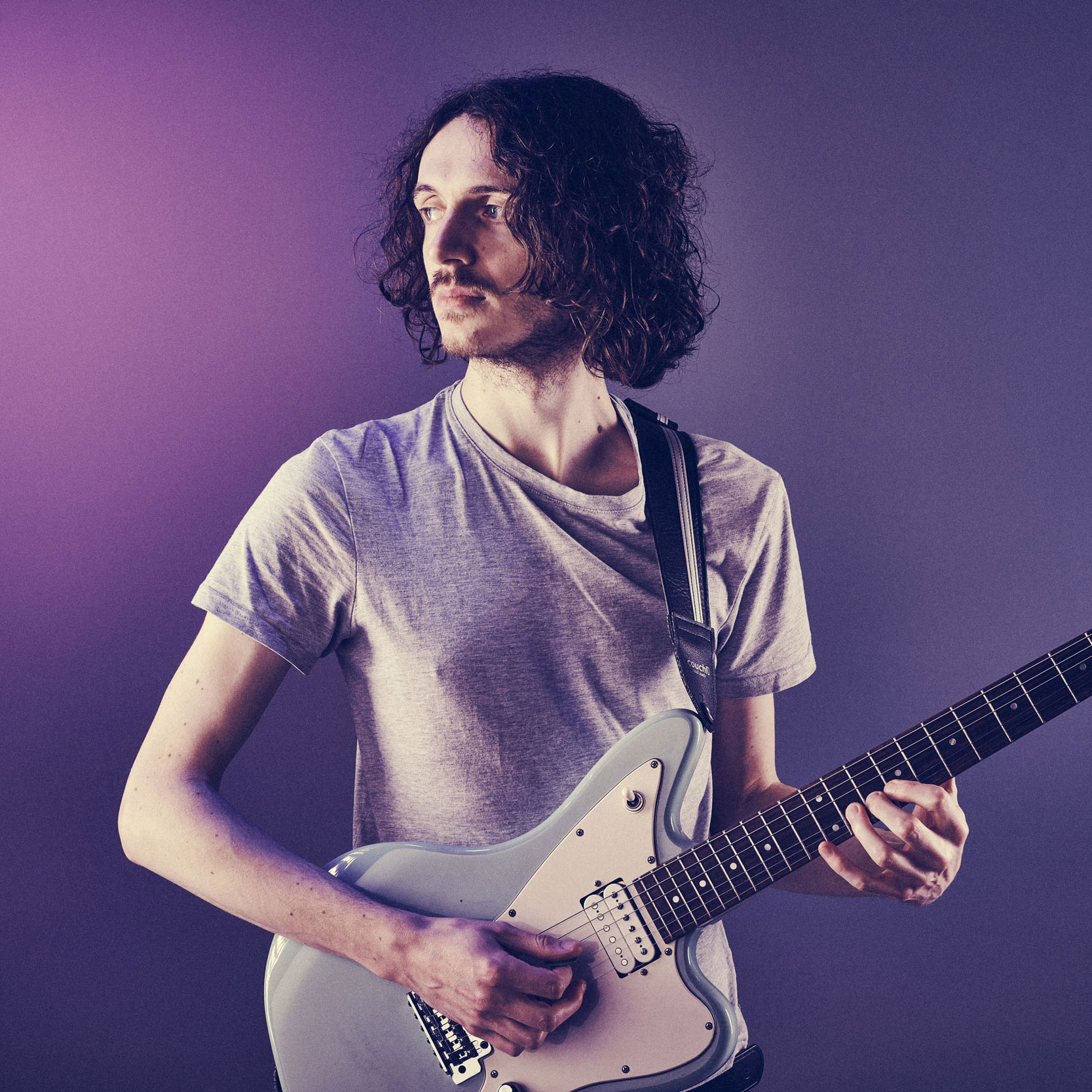
Mike is Editor-in-Chief of GuitarWorld.com, in addition to being an offset fiend and recovering pedal addict. He has a master's degree in journalism from Cardiff University, and over a decade's experience writing and editing for guitar publications including MusicRadar, Total Guitar and Guitarist, as well as 20 years of recording and live experience in original and function bands. During his career, he has interviewed the likes of John Frusciante, Chris Cornell, Tom Morello, Matt Bellamy, Kirk Hammett, Jerry Cantrell, Joe Satriani, Tom DeLonge, Ed O'Brien, Polyphia, Tosin Abasi, Yvette Young and many more. In his free time, you'll find him making progressive instrumental rock under the nom de plume Maebe.
You must confirm your public display name before commenting
Please logout and then login again, you will then be prompted to enter your display name.
“It holds its own purely as a playable guitar. It’s really cool for the traveling musician – you can bring it on a flight and it fits beneath the seat”: Why Steve Stevens put his name to a foldable guitar
“Finely tuned instruments with effortless playability and one of the best vibratos there is”: PRS Standard 24 Satin and S2 Standard 24 Satin review