Bigsby vibrato tailpiece: everything you need to know about the iconic tremolo system
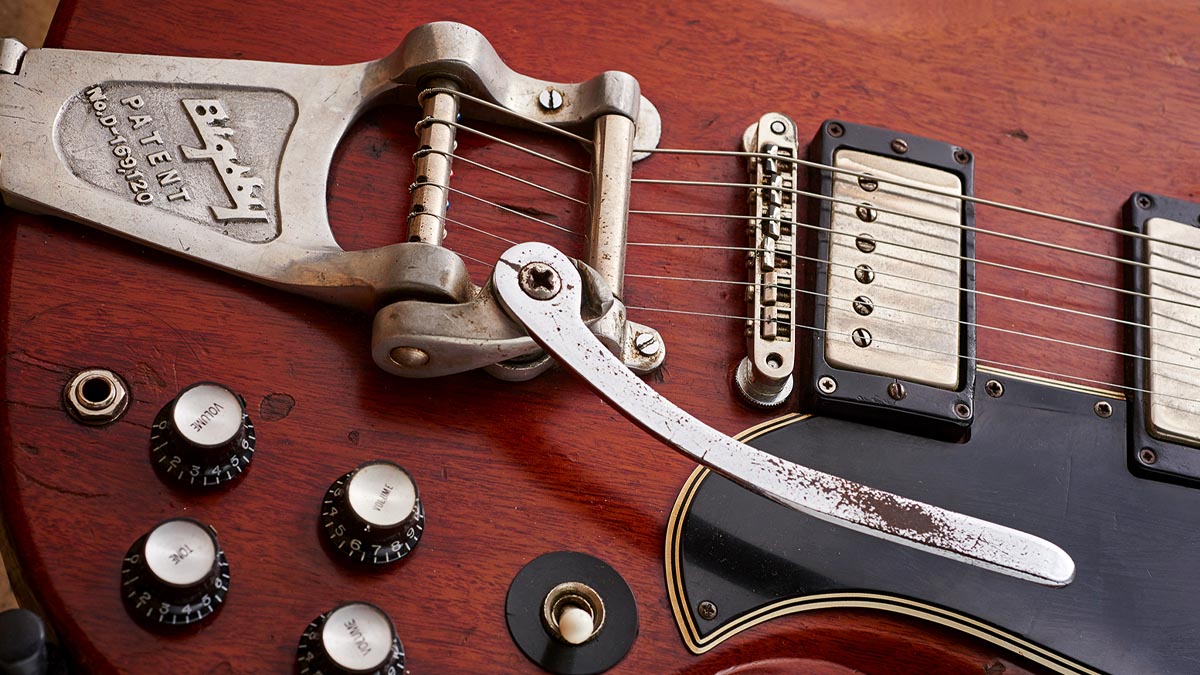
Bigsby vibratos were the must-have accessories for pioneering country pickers, rockabilly tearaways and 1960s psychedelic blues experimentalists. These days, they’re as popular as ever with indie rockers and ambient noiseniks.
That’s quite remarkable for a product that has remained essentially unchanged since 1951 – but Bigsby vibratos simply work because they work simply.
There was clearly demand for a mechanical guitar vibrato device long before Paul Bigsby turned his attention to it, and if you were a pro player then that probably meant a Kauffman Vibrola.
Clayton Orr ‘Doc’ Kauffman came up with his design back during the 1930s when he worked for Rickenbacker, and he subsequently co-founded K&F Manufacturing Corporation with his close friend Leo Fender.
Kauffman Vibrola users included Les Paul, Chet Atkins and Merle Travis, and it was Travis who first approached Paul Bigsby to repair the problematic Vibrola on his Gibson L-10. The repair wasn’t a complete success, so Travis encouraged Bigsby to design and build his own vibrato device instead.
How Bigsbys Work
Paul Bigsby was a ‘fix anything, build anything’ kind of guy and he started out designing and building parts for motorcycles. Much of his work involved casting and machining metal, and he was certainly influenced by Rickenbacker’s aluminium ‘frying pan’ guitar.
When Bigsby moved into instrument manufacturing, he combined figured maple with tooled aluminium components. His vibrato design was largely derived from his biking background, but it also incorporates some elements of traditional instrument making.
Get The Pick Newsletter
All the latest guitar news, interviews, lessons, reviews, deals and more, direct to your inbox!
Prior to the solidbody era, electric guitar players were still playing big-bodied archtops. Strings were typically anchored on a tailpiece that folded around the edge of the body and was secured against the tailblock. Bigsby replaced the tailpiece with a solid casting that attached in the same way but rested on top of the body, rather than floating above it.
The Kauffman Vibrola rocked side to side, but Bigsby realised he could achieve a vibrato effect by allowing the string anchor points to rotate forwards and backwards. Of course, the ability to return to pitch accurately is a basic requirement for any vibrato system, and Bigsby employed a couple of common engineering components to achieve this.
He would have been more than familiar with bearings and springs from his work with motorcycles. Low friction is critical, so the main section of Bigsby’s vibrato has two large holes drilled into the aluminium casting to accommodate a pair of roller bearings. A bar with string-securing pins slots through these bearings and is secured at one end by a circlip.
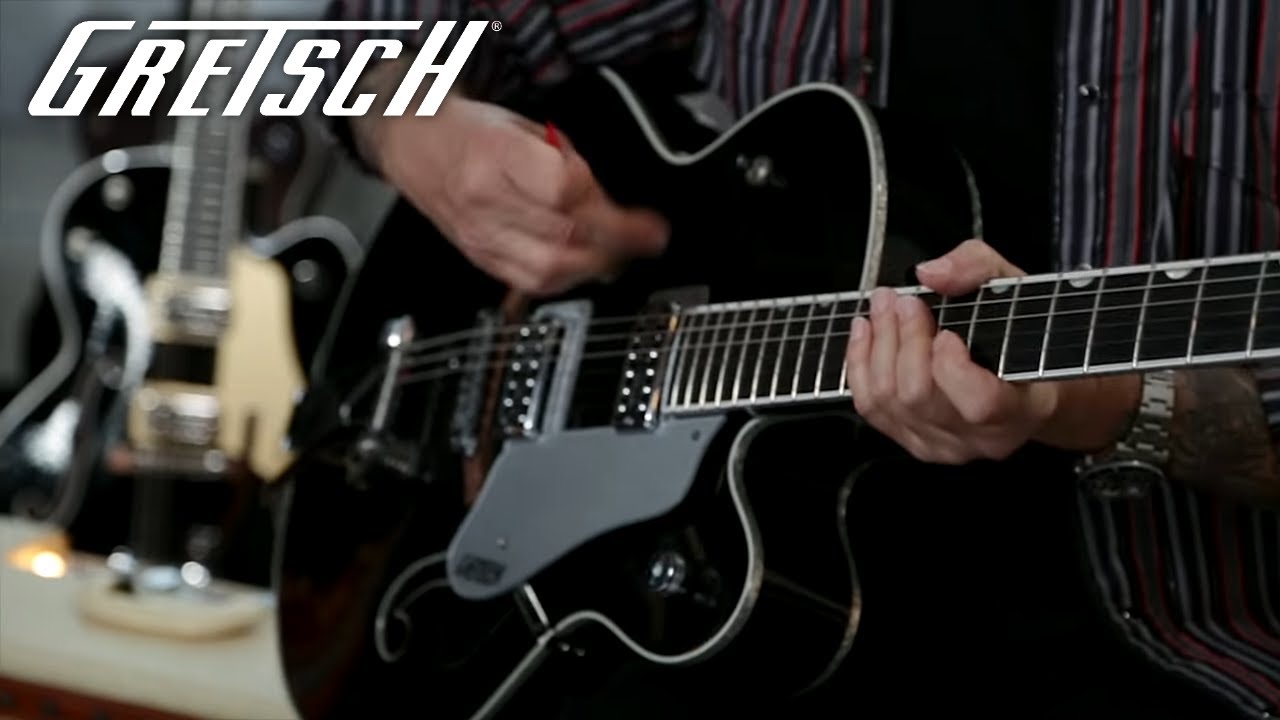
Bigsbys have a robust spring to counteract the string tension. The main moulding incorporates a small cup for the spring to sit in and a bracket, attached to the string bar with a grub screw, rotates forward to cover the top of the spring.
With the strings tuned up to pitch, the tension keeps the whole assembly pressed tightly against the guitar body and the bracket applies sufficient downwards pressure to hold the spring in place. The spring is calibrated to counteract string tension, while remaining soft enough to compress when the handle attached to the bracket is pressed downwards.
Ultimately, the Bigsby vibrato is a mechanical engineering solution to a musical problem. As such, it blazed a trail for many of the guitar hardware innovations that followed over the following decades.
Model Variations
In the rapidly evolving electric guitar scene of the early 1950s, Paul Bigsby’s ‘one size fits all’ approach soon became unsustainable. For smaller semi-solid archtops, such as the Gretsch Duo Jet, Bigsby introduced a shorter version of the B6 with a scaled-down hinge called the B3.
During the 1960s, Bigsbys were so popular that production was farmed out to Selmer, who built them under licence in the UK
For guitars with lower arches and flat tops, such as Les Pauls and various ES models, the B7 features a front roller bar to increase the string break angle over the bridge, and it has to be screwed onto the top.
The B5, nicknamed the ‘Horseshoe Bigsby’, also features a front roller but no hinge. Designed to be screwed onto the front of flat-topped guitars, it suits SGs, Telecasters, Juniors, Rickenbackers and Firebirds.
Bigsby even designed a vibrato specifically for Telecasters. With integrated bridge pickup mounting and a cutout for a drop-in bridge, the B16 is impressive, but it’s a big commitment and there are other options that preserve more of the authentic Tele tone and vibe.
During the 1960s, Bigsbys were so popular that production was farmed out to Selmer, who built them under licence in the UK. Bigsby also made branded versions for Gretsch and Guild.
By 1965, health issues forced Paul Bigsby to sell his company to former Gibson president Ted McCarty. Fred W Gretsch purchased Bigsby in 1999 and two decades later Bigsby was acquired by its current owner, the Fender Musical Instruments Corporation.
Modular Mods
The basic Bigsby design has remained unchanged, but as a modular system it’s possible to swap some components in order to modify the feel and enhance playability.
For example, Bigsbys have been offered with a variety of handles, which are very easy to swap. Simply slacken off the grub screw that’s securing the bracket to the pin bar using an Allen key. Popular options include the Merle Travis, Chet Atkins/Wire Arm, Duane Eddy and vintage wide handles.
Some players, including Darrel Higham, prefer the original non-swivel-style fixed handle, but it comes down to personal taste. You can also adjust the ‘swivel-ability’ of your handle by tightening or loosening its fixing screw. But if it’s set too loose, the vibrato may feel less responsive and precise.
The spring’s height and stiffness affect the feel of the vibrato and the height of the handle. Again, it’s really a matter of taste, but some players prefer the softer feel of the Reverend spring.
Bear in mind that a softer spring may compress when you bend strings – just like a three-spring Strat setup. If you like the feel of your spring but would like your handle to be a bit higher, try placing a coin under the spring. It will need to be wider in diameter than the spring but narrower than the ‘cup’ that the spring sits in.
Owners sometimes struggle to hook strings onto the pins of Bigsby-equipped guitars. In recent years, ‘pinless’ Bigsbys have been introduced to allow through-bar stringing. You can remove the pins and drill out the bar for through-stringing, but it’s safer and easier to retrofit a Callaham pinless bar or a Vibramate String Spoiler.
Elsewhere, some find that Bigsbys with front rollers have compromised sustain and frequency response. If you feel that way, check out the Callaham Front Roller upgrade kit. This direct replacement is made from stainless steel and is claimed to improve sustain and tuning stability.
Front rollers can induce a very sharp break angle over the bridge, which may prevent the strings from sliding freely over it. The BiggsFix Tuning Stabilizer mounts into the existing roller holes, but it’s raised up to soften the break angle and improve tuning stability.
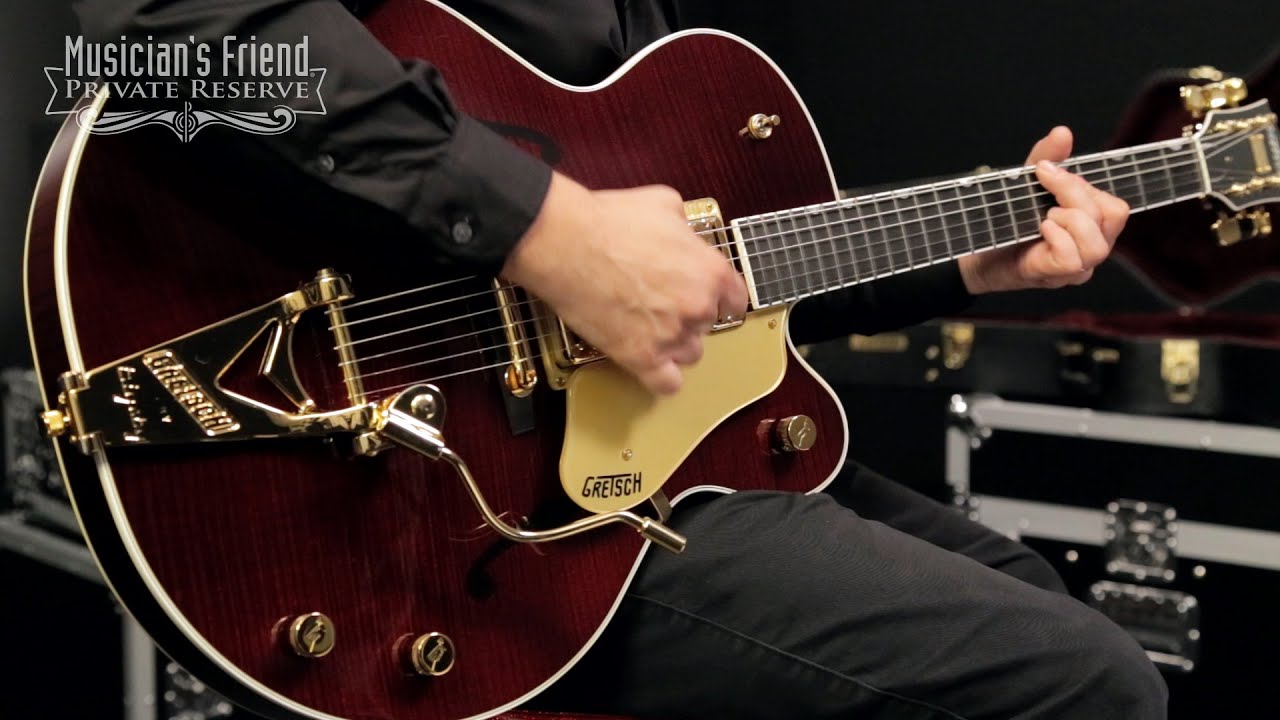
If you want to retrofit a Bigsby to a stop tailpiece guitar but you’re reluctant to drill holes into the body, check out the Vibramate range of products. They offer non-destructive Bigsby-mounting systems for Les Pauls, SGs, ES models, Telecasters, Flying Vs and more besides.
Also investigate the Towner product range, which includes a Down Tension Bar that mounts onto stop tailpiece bushings and enables the use of B3 and B6 Bigsbys on guitars that would otherwise need a front roller Bigsby.
It also offers a hinge-plate adaptor that allows solid fixing via the strap-button screwhole, plus spacer blocks for extra mounting options on various guitars, including Firebirds.
Maintenance Tips
So long as you understand their limitations, Bigsbys are reliable and stable. If you do experience tuning issues when using one, you can usually trace the problems to the bridge, bridge saddles, nut or tuners, rather than the Bigsby itself. You should also ensure the unit sits properly on top of the guitar and doesn’t rock from side to side. The use of additional felt spacer pads may be needed if it does.
Very old Bigsbys can stiffen up due to congealed grease, dried-up oil and dirt accumulation. It usually takes years (or even decades) for these issues to manifest, though, and plenty of ancient Bigsbys still work perfectly.
Bigsbys are reliable and stable. If you do experience tuning issues when using one, you can usually trace the problems to the bridge, bridge saddles, nut or tuners
Next time you remove your strings, try turning the pin bar and front roller (if you have one) by hand. Both should spin freely with no resistance, but if that isn’t the case, it’s clean-up time. You’ll need an Allen key to remove the grub screws securing the string pins, plus circlip pliers to release the pin bar.
With the circlip and grub screws now removed, the pins can be pushed out of the bar and the bar will slide out of the casting. You’ll see roller bearings mounted in the casting, and these should be flushed out with naphtha (aka lighter fluid – so don’t forget to work in a well-ventilated area).
Once they’ve dried off, apply fresh lithium grease to the bearings and wipe off any excess. The pin bar will most likely be sticky, too; if this is the case, you can clean it with naphtha or acetone. Follow up with some chrome polish in the areas where the bar contacts the bearings.
Front rollers are secured by a grub screw on the underside of the casting and you can use an Allen key to remove it. The central bar can be pulled out of the casting and separated from the roller tube, which has bearings at each end.
Soak both parts in naphtha until all the old oil and grease can be removed, polish the bar and apply fresh grease to the bearings before reassembly. The whole process shouldn’t take more than a couple of hours, and your Bigsby should be good for another decade or so.
Huw started out in recording studios, working as a sound engineer and producer for David Bowie, Primal Scream, Ian Dury, Fad Gadget, My Bloody Valentine, Cardinal Black and many others. His book, Recording Guitar & Bass, was published in 2002 and a freelance career in journalism soon followed. He has written reviews, interviews, workshop and technical articles for Guitarist, Guitar Magazine, Guitar Player, Acoustic Magazine, Guitar Buyer and Music Tech. He has also contributed to several books, including The Tube Amp Book by Aspen Pittman. Huw builds and maintains guitars and amplifiers for clients, and specializes in vintage restoration. He provides consultancy services for equipment manufacturers and can, occasionally, be lured back into the studio.
“Wins out on battery life, stealthy aesthetics and its well-judged Cable Tone feature”: Blackstar Airwire i58 review
“A distinctive brightness that no other strings have been able to capture”: How Rotosound revolutionized the bass world with its Swing Bass 66 strings – and shaped the sound of rock music in the process