30 years of Eastman: revisiting the golden age of handcrafted guitar making
The history of Eastman Musical Instrument Company reads like a three-decade sprint through the evolution of stringed instruments, and it is a story shaped by hand tools and old-school craft
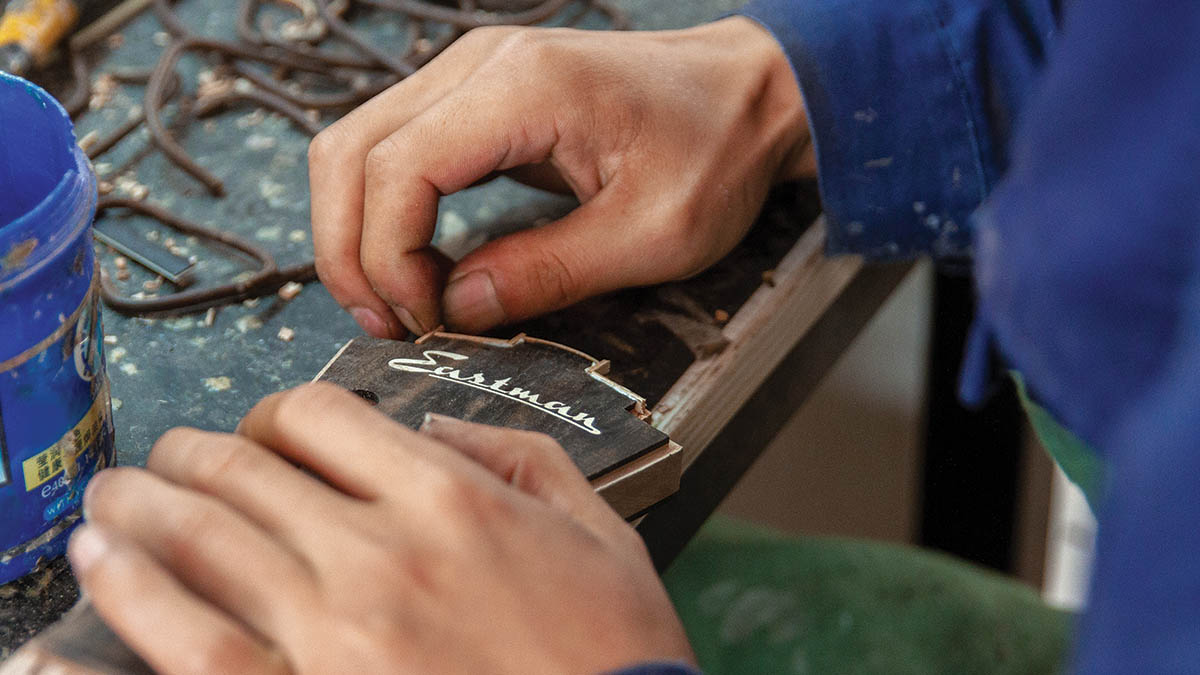
The history of the Eastman Musical Instrument Company is like condensing the 300-year evolution of stringed instrument design into only 30 years with a focus on the greatest achievements and breakthroughs.
Founder Qian Ni started Eastman in 1992 with the goal of building high-quality yet affordable violins, violas, cellos and string basses using traditional craftsmanship and techniques.
The success of those efforts eventually inspired Ni to start producing archtop guitars and mandolins in 2002, followed by steel-string acoustic flattops in 2008, thinline electrics in 2012 and solidbody electric guitars in 2016.
“We have redone the golden age of guitar building,” says Eastman International Sales and Product Development Manager of Fretted Instruments Pepijn ’t Hart. “But it all came naturally. From the beginning, our focus was to use traditional building techniques to provide the best possible instruments that anyone could afford.
“As Eastman grew, it became very important for us to offer a wider range of instruments. It was actually very logical for us to go from making violins to making archtops and mandolins and then progress to flattops, thinline electrics and solidbodies in much the same way that things progressed naturally over history.”
Although Eastman’s founder Qian Ni is Chinese and the company’s instruments are manufactured in China, Ni and his company’s story reads more like a tale of the American dream ripped from the pages of a Horatio Alger novel.
After Ni graduated from Boston University School of Music, he started a business importing and selling student-grade classical stringed instruments that he loaded into his car and delivered himself to violin and music stores across the U.S.
Get The Pick Newsletter
All the latest guitar news, interviews, lessons, reviews, deals and more, direct to your inbox!
Instead of just trying to sell off his merchandise, Ni listened closely to retailers’ complaints about the poor quality of the modern machine-made instruments. The main problems were that affordable violins were inferior and quality instruments were prohibitively expensive.
This situation inspired Ni to start his own company that manufactured stringed instruments. As a music scholar, he was familiar with the German luthier traditions of the 17th and 18th centuries, which were based on the guild system.
Ni decided to model his factory after that approach combined with modern assembly line techniques to enable him to produce instruments at a lower cost.
In essence, Ni assembled a team of specialists, each assigned to a specific task that they excelled at individually, such as shaping necks, carving tops and backs and applying finishes. Most of the work was – and still is – done using hand tools like chisels, files, gouges and planes. As a result, Eastman was able to produce truly hand-crafted instruments for affordable prices.
Eastman’s eventual progression to building archtop guitars was essentially a happy accident.
“I was given a book about archtop guitars as a gift,” Ni says. “Immediately I became interested in the similarities between archtop guitars and our violins, violas, cellos and basses.
“As we began learning about these guitars we discovered not only the crossover in building techniques but also the rich history of luthiers who built violins and guitars. C.F. Martin, Lloyd Loar of Gibson and John D’Angelico all had experience in violin making. Antonio Stradivari even built some guitars!
“We started talking to different luthiers for advice and ultimately used Bob Benedetto’s book about archtop guitar construction to build our first guitars.
“When we brought our first archtop guitars to the NAMM Show in 2002, the excitement that they generated was contagious,” Ni continues. “That was definitely a pivotal moment for us. We have been so fortunate to work with so many talented people who have helped us along the way, and it all started with the reception we got at the NAMM Show.”
Eastman’s archtop guitars quickly earned acclaim from discriminating guitarists like Frank Vignola and John Pisano and luthiers like Claudio Pagelli and Otto D’Ambrosio, who collaborated with the company on archtop models and designs.
Our new Romeo is D’Ambrosio's design, which was our first step in making a thinline model that was truly our own
Pepijn ’t Hart
“Qian has always reached out to talented designers to collaborate,” Hart says. “He would meet people at guitar shows and ask if they could do something together. Rudy Pensa (retailer, Rudy’s Music in New York) has remained an important advisor since the very start when we first offered archtops.
“Back in 2002 when Eastman was starting to build archtop guitars, Qian reached out to Otto D’Ambrosio, who is a talented designer who got his start as an apprentice for (luthier/repairman) Flip Scipio and (archtop luthier) John Monteleone and built guitars for Guild at their Westerly factory before starting his own business.
“In 2014 he decided to work full time for Eastman, and he is now our head designer. Our new Romeo is his design, which was our first step in making a thinline model that was truly our own. Now we’re working on new solidbody designs, including our first offset body shape with six-on-a-side tuner headstock design.”
The next logical step for Eastman was to start building flattop steel-string guitars, which the company introduced in 2008. The company’s experienced craftsmen combined with the input of various collaborators enabled Eastman to quickly expand their customer base and reputation as a builder of high-quality affordable instruments.
Eastman’s line of flattop guitars is impressively extensive, encompassing traditional models from parlor to jumbo sizes, the modern AC series Grand Auditorium designs and even uncommon variations like the vintage Selmer-style Gypsy Jazz and nylon-string Cabaret-JB developed with luthier John Buscarino.
You cannot get more traditional than our E20D-TC dreadnought. It has the look, feel and tone of a Thirties dreadnought instrument
Pepijn ’t Hart
While many of Eastman’s flattop models are inspired by designs from the 1930s “Golden Age,” these guitars offer many improvements and innovations that allow the instruments to stand on their own merits.
“Whenever we design an instrument, we hope that we can offer musicians something new,” Hart says. “For example, you cannot get more traditional than our E20D-TC dreadnought. It has the look, feel and tone of a Thirties dreadnought instrument, but a big part of the reason for that is because the spruce top is thermo-cured, which is what the TC stands for. We have our own kilns that we use to torrefy woods.
“Then there are models like the AC722CE,” he continues. “It’s a modern Grand Auditorium flattop with a cutaway, side sound port, beveled lower bass bout and built-in pickup, which are all beautiful small details that show off our craftsmanship. It also features the Tonetight detachable neck mounting system, which was developed by Dana Bourgeois, who we started a partnership with in 2019.”
Eastman’s partnership with Bourgeois immediately paid dividends. “We have learned a great deal from Dana about the finer details of flattop guitar production,” Hart says. “He showed us things like how making the tops a little thicker and the braces a little thinner makes a huge difference in sound, which we’ve now implemented in our workshop.
Last year we stopped shooting nitrocellulose finishes, which is something we’ve wanted to do for a long time since it’s not great for the environment or the workers who spray it
Pepijn ’t Hart
“Last year we stopped shooting nitrocellulose finishes, which is something we’ve wanted to do for a long time since it’s not great for the environment or the workers who spray it. It’s unhealthy, but unfortunately many players still preferred nitrocellulose finishes so we continued to offer them.
“Dana told us that he stopped using nitrocellulose in 2002 and started using a special formula that he developed, which he shared with us. Last year we completely changed over to what we call the Truetone finish, which is very thin polyurethane with a lot of the same qualities as nitro. We did comparison tests all over the world, and no one could tell the difference in feel or tone between a nitro finish and our Truetone finish.”
Although Eastman’s thinline and solidbody electric models are relatively recent additions to the company’s offerings, these instruments have benefitted from the know-how acquired preceding their introductions as well recent developments like the Truetone finish.
The variety of thinline models produced by Eastman is particularly distinctive, as they offer an all-solid carved series (solid top, back and sides), solid carved top series (solid spruce top and laminated back and sides) and laminate series (laminated top, back and sides) thinline guitars, whereas most companies only manufacture laminate thinline guitars.
Eastman’s solidbody models resemble several classic Gibson Les Paul models from the Fifties, but there are a few significant differences.
“We introduced our first solidbody model, the SB59, in 2016,” Hart says. “Although it’s a single cutaway solidbody guitar with an arched maple top over a mahogany body, we weren’t looking to duplicate the sound of a Les Paul. First of all, our model is lighter. The SB59 never weighs more than eight pounds, so it’s much more comfortable to play.
“I wanted the SB59 to have a sound that was more airy and brighter, so I approached Jason Lollar to design a new pickup for us. He came up with the Eastman Imperial humbucker, which was a perfect fit. As a result, most players are finding the SB59 more versatile than a traditional Les Paul design.”
Similar to how Eastman’s flattop designs have progressed from models inspired by the classics to the introduction of models with modern, innovative features, the company’s thinline and solidbody models are progressing as well.
The Romeo thinline is Eastman’s first electric model to offer a glimpse of what lies ahead. Head designer Otto D’Ambrosio came up with the main concept for the Romeo model, although the final specs came together somewhat by accident.
“At first, Otto showed me a design for an archtop thinline model,” Hart says, “but I didn’t want another jazz guitar. Also, the materials were close to what we already offered – a mahogany neck, solid mahogany back and sides, maple top, two humbuckers.
“In 2018, Otto and I traveled to the workshop to check on prototypes, and our head builder told us that they were having trouble getting mahogany that was good enough quality for routing out the back and sides from a single piece. He asked if he could use laminated mahogany instead, and we decided to give that a try.
“When they made the next prototype, they also switched the top from solid maple to solid spruce and switched the neck from mahogany to maple. None of these new changes were asked for, so it turned out to be a freak accident. When the guitar came in, I started playing it and thought it was unbelievable.
“I could do everything from bright Telecaster tones to warm jazz tones on it, but it also had a unique voice that was all its own. Suddenly, it made perfect sense to me, and we pushed for it. Shortly afterwards, Qian walked by and saw the guitar, and he said, ‘That’s the future of our guitars.’ As always, he was absolutely correct.”
Even though Eastman has grown significantly over the last 30 years, the company still builds its instruments by hand, using power tools only when they are absolutely necessary. As demand for Eastman guitars has increased, that presented a few challenges.
“There is no button we can push that allows us to build more instruments at once,” Hart says. “The majority of our building process is done by hand, which is something we are very proud of and don’t want to change. That is truly the unique characteristic of an Eastman.
“Sometimes customers will want us to duplicate the neck on an Eastman model they own, but we can’t really do that as all of our necks are shaped by hand and every neck has a specific individual feel.”
We are always trying to improve and be better at what we do. We always have to balance what we want to do with what we can actually do
Qian Ni
Eastman has covered impressive ground in its 30 years – after all, duplicating 300 years of stringed instrument development in that timespan is no small feat. However, even though the company has made many notable achievements over that time, Qian Ni says he looks forward to the growth that lies ahead.
“As a relatively young company we are always learning, which is a gift and challenge,” he says. “We are always trying to improve and be better at what we do. We always have to balance what we want to do with what we can actually do. So far it’s worked out well, and we are excited for the next 30 years.
“Our philosophy has been to try to build the highest-quality instruments for beginning students to professional musicians. We are a people-first company. Our team around the world is the heart and soul of Eastman.”
Chris is the co-author of Eruption - Conversations with Eddie Van Halen. He is a 40-year music industry veteran who started at Boardwalk Entertainment (Joan Jett, Night Ranger) and Roland US before becoming a guitar journalist in 1991. He has interviewed more than 600 artists, written more than 1,400 product reviews and contributed to Jeff Beck’s Beck 01: Hot Rods and Rock & Roll and Eric Clapton’s Six String Stories.